OPP-200
Shaker
Our state-of-the-art shaker motor boasts a dual-rotation capability. Clockwise rotation is optimized for screening maximal material during standard padding operations, while its counter-clockwise functionality is tailored for downhill padding, ensuring the efficient clearance of materials from the shaker screen. Integrated hydraulic actuators, situated at the rear of the shaker system, enable precise modulation of the shaker's height and angular position, all while maintaining independence from the conveyor. This design empowers the operator to adeptly adjust the shaker's elevation, especially during operations on inclined terrains, thus optimizing material throughput.
Additionally, a vibrator, strategically positioned beneath the spill pan, can be activated to effectively dislodge debris in environments characterized by wet or densely packed materials.
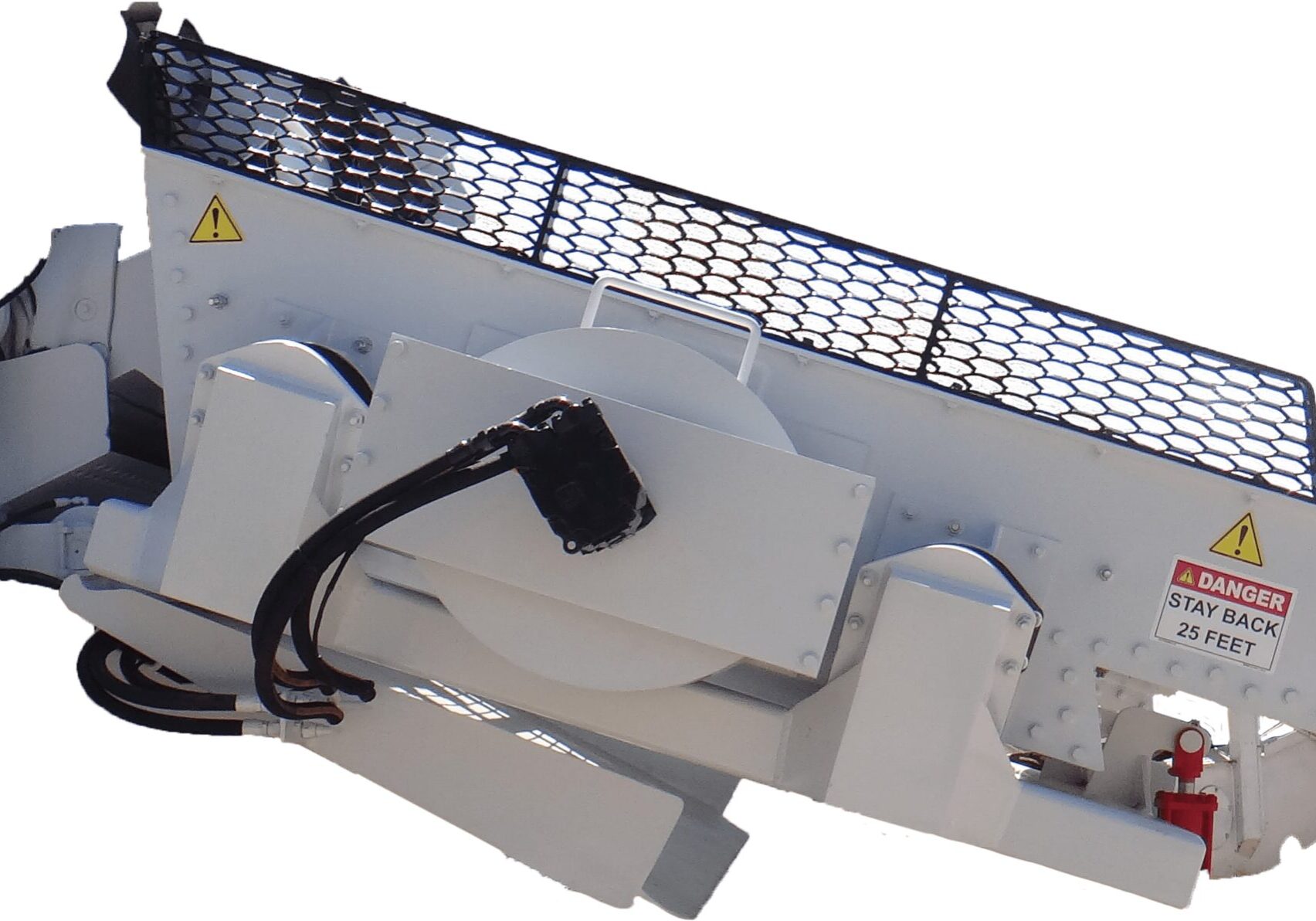
Engine
The unit is propelled by the sophisticated six-cylinder Liebherr D936 LA6 engine, meticulously engineered to endure extreme temperature variations and high-altitude conditions.
The D936 engine exemplifies superior engineering attributes, including an exceptional power-to-weight ratio, extended operational longevity, peak efficiency, minimal vibrational disturbances, and an impressive torque range.
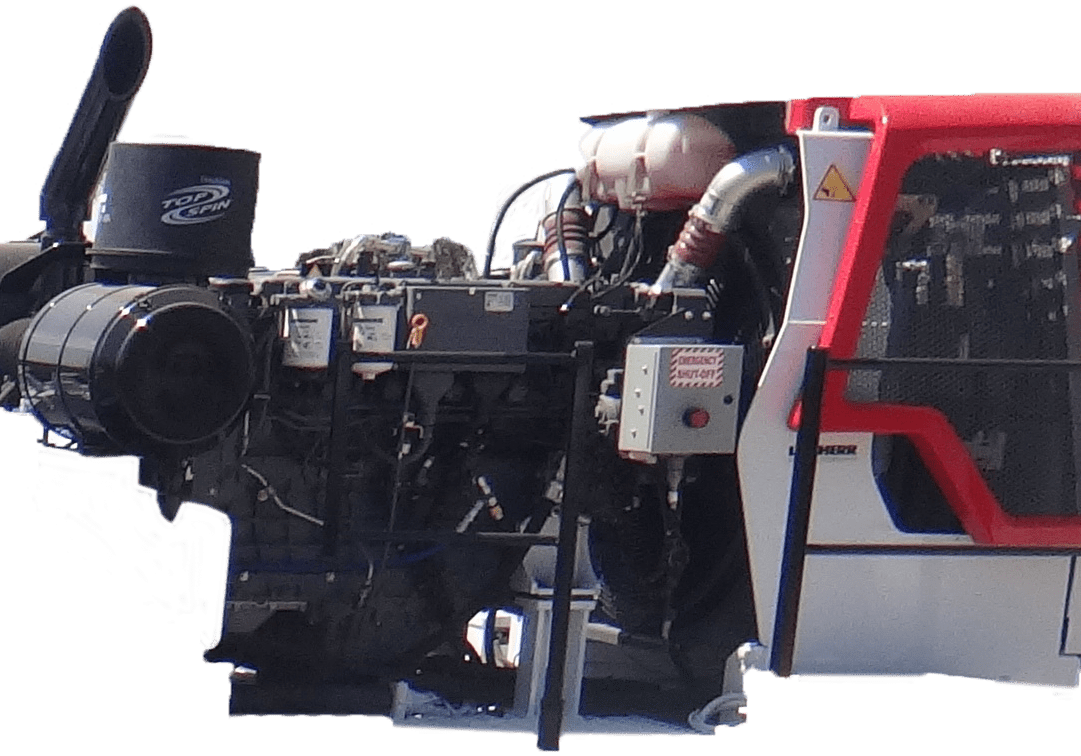
Screen Size
The OPP-200 series accommodates screen sizes spanning from 1/4" to 4", with the provision for adjustments in precise 1/4" increments.
Each screen undergoes meticulous accuracy evaluations, guaranteeing consistent and exact material filtration in every application.
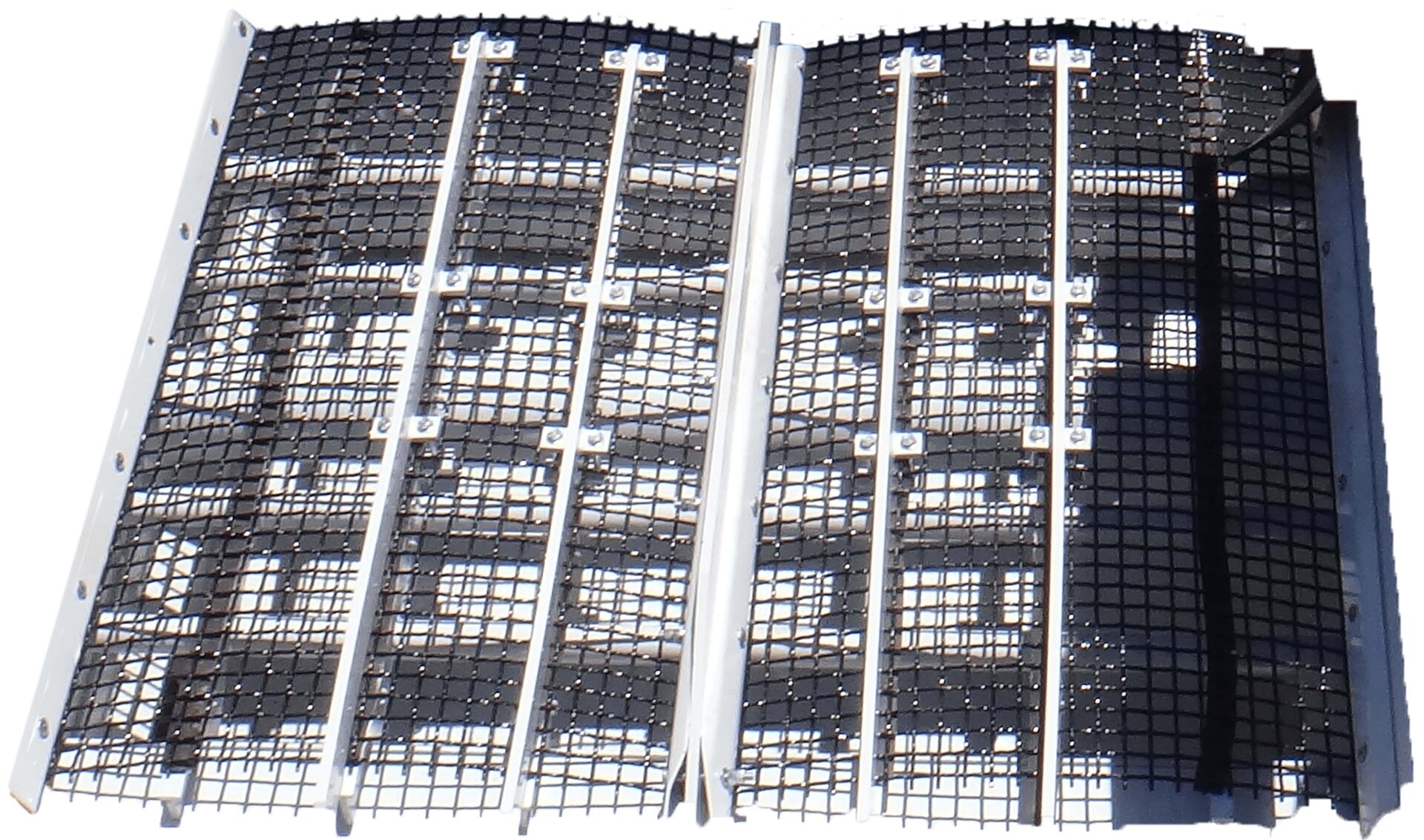
Video Monitoring System
Four high-definition, anti-glare color cameras ensure vivid imagery even under direct sunlight. The camera housings are nitrogen-purged to deter dust intrusion, and the enclosures are engineered to prevent condensation, frost, and moisture infiltration. Integrated shock absorbers mitigate the effects of impacts and vibrations, while robust protective casings shield against potential damage from falling debris.
Within the cabin, three state-of-the-art monitors provide operators with comprehensive visual coverage; showcasing views down the elevator, of the conveyor output, and the machine's left flank. Additionally, a rear-facing camera system activates an ensemble of six cameras during reverse maneuvers, enhancing operational safety.
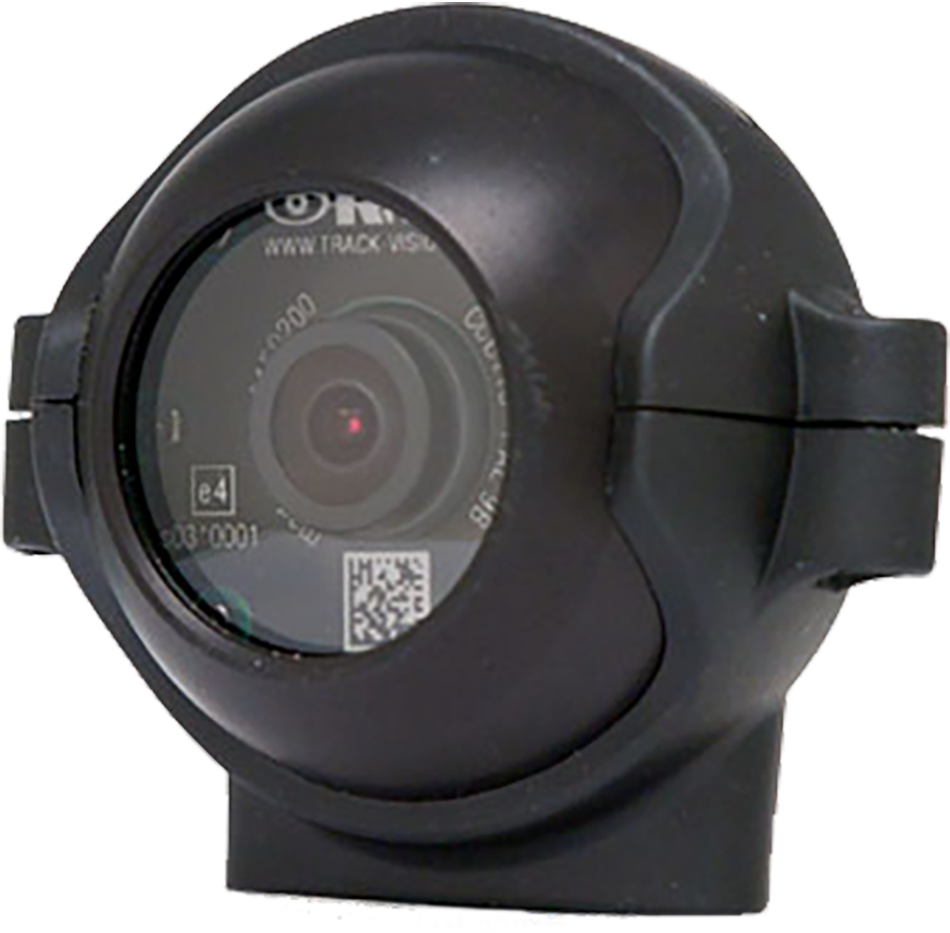
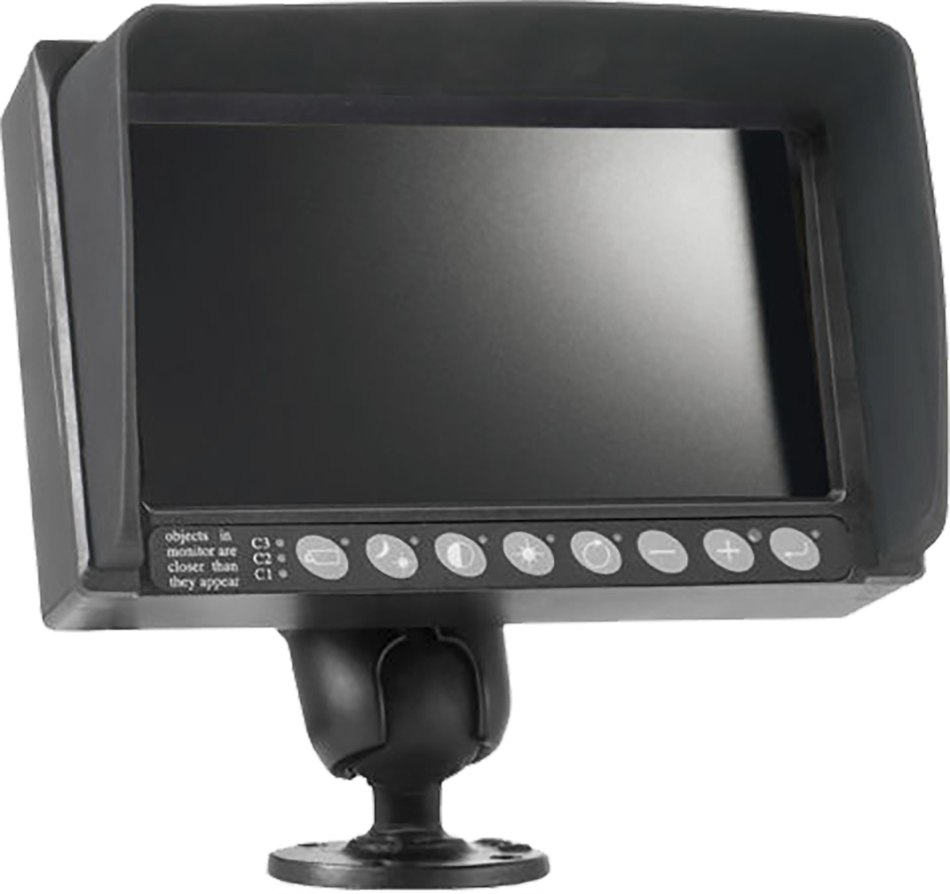
Video Monitoring System
Four high-definition, anti-glare color cameras ensure vivid imagery even under direct sunlight. The camera housings are nitrogen-purged to deter dust intrusion, and the enclosures are engineered to prevent condensation, frost, and moisture infiltration. Integrated shock absorbers mitigate the effects of impacts and vibrations, while robust protective casings shield against potential damage from falling debris.
Within the cabin, three state-of-the-art monitors provide operators with comprehensive visual coverage; showcasing views down the elevator, of the conveyor output, and the machine's left flank. Additionally, a rear-facing camera system activates an ensemble of six cameras during reverse maneuvers, enhancing operational safety.
Machine Specifications
Machine Dimensions
Transport Dimensions
Working Dimensions
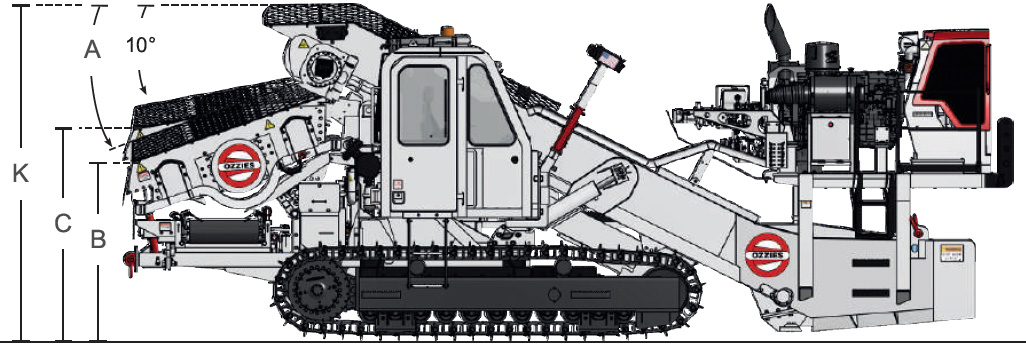
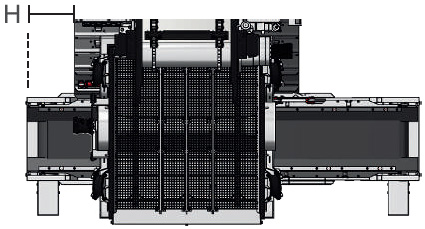
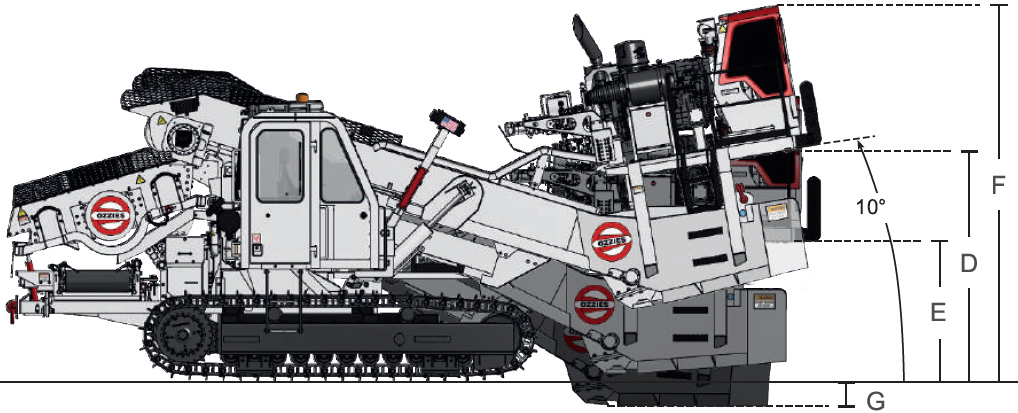
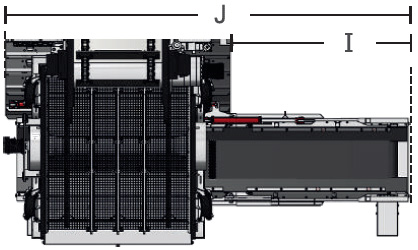
A | Maximum shaker angle from ground | 17° |
B | Minimum shaker height | 72.24" |
C | Maximum shaker height | 96" |
D | Raised scoop clearance | 97.32" |
E | Normal scoop clearance | 60.36" |
F | Total machine height with elevator raised | 168.36" |
G | Cutting edge diving depth | 24" |
H | Maximum conveyor reach, non-operator side | 24.96" |
I | Maximum conveyor reach, operator side | 108.84" |
J | Maximum overall width | 217.08" |
Minimum overall width | 192" | |
K | Height | 132.36" |
Main Applications
Backfill separation is a critical practice in pipeline projects, contributing to the reliability, safety, and cost-effectiveness of pipeline infrastructure installation and maintenance. It supports proper pipeline protection, minimizes the risk of damage, aids in erosion control, ensures environmental compliance, and enhances overall project efficiency.
Backfill separation plays a crucial role in renewable construction, maintenance, and environmental compliance. It enhances the stability and longevity of foundations, reduces cable damage risks, mitigates erosion, and contributes to cost-effective and environmentally responsible renewable operations.
Backfill separation is a critical practice in electrical transmission projects, contributing to the reliability, safety, and cost-effectiveness of high-voltage transmission lines and associated infrastructure. It supports proper foundation construction, minimizes cable damage risks, aids in erosion control, ensures environmental compliance, and enhances overall project efficiency.
Backfill separation is essential in utility projects, contributing to the reliability, safety, and cost-effectiveness of utility infrastructure development and maintenance. It facilitates proper installation and maintenance, minimizes the risk of damage, supports erosion control, ensures environmental compliance, and enhances overall project efficiency.