MINI-PADDER
Conveyor
Inside the cabin, sophisticated control mechanisms grant comprehensive oversight over the rotation direction, velocity, and maneuvering of the Mini-padder conveyor. These nuanced controls enable exact modulation of the screened material's flow.
For enhanced mobility, the conveyor has been engineered to fold seamlessly, particularly beneficial for transportation and navigation within restricted environments, subsequently minimizing deployment durations.
The conveyor's lateral movement is governed by a dedicated motor, ensuring precision in material placement within the ditch. The conveyor's distinctively architected contour optimizes the dispersion radius of the material.
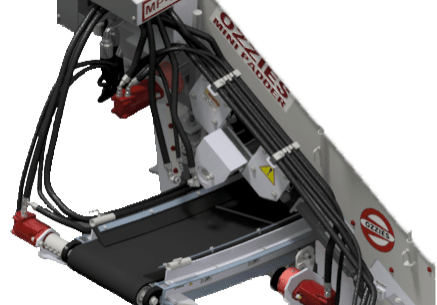
Controls
The controls for Ozzie's Mini-padder have been strategically situated on the dedicated control box, adjacent to the loader arm control mechanisms.
This control box hosts an array of meticulously labeled operational components:
- Master Hitch Pin Activation
- Master Hitch Depin Functionality
- Conveyor Lateral Movement Toggle Switch
- Elevator Speed Variability Dial
- Conveyor Speed Adjustment Interface
- Vibrator Intensity Modulation
- Temporary Elevator Reversal Toggle Switch
- Conveyor Directional Toggle Switch
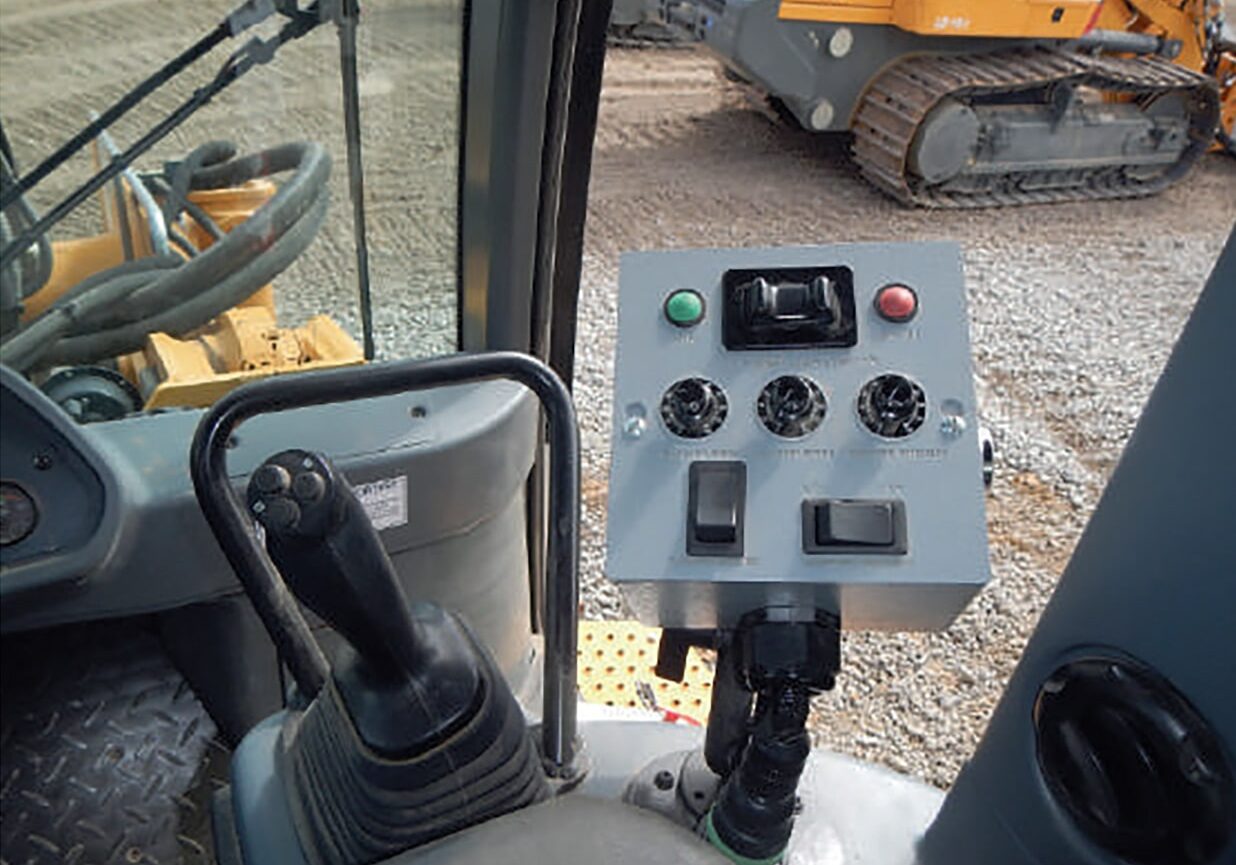
Elevator
Through meticulous engineering and exhaustive testing, we guarantee that Ozzie's Mini-padder screens precisely to the stipulated dimensions. Our proprietary adjustable elevator drive system is designed to provide consistent chain engagement, significantly minimizing undesired shifts and slips.
Externally positioned variable chain adjusters on the padding head facilitate optimal chain tension management, especially in challenging terrains. Furthermore, the integrated chain vibrator, which can be activated instantaneously, is adept at screening dense or moist materials, while simultaneously dislodging debris from the chain.
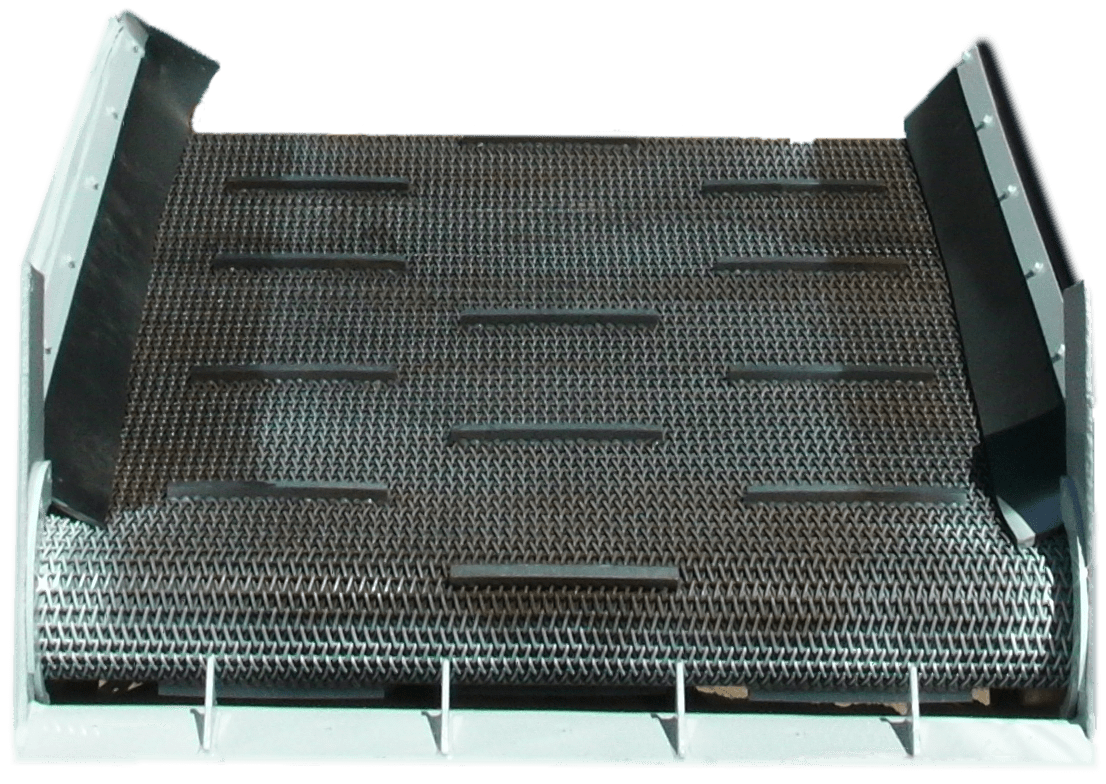
Machine Specifications
Machine Dimensions
Padder Dimensions
Main Applications
The Mini-padder has been engineered to facilitate the precise backfilling of narrow diameter trenches, encompassing dimensions ranging from 3 to 10 inches (76 to 254 mm) in diameter.
Backfill separation is a critical practice in distribution cable projects, contributing to electrical distribution systems' reliability, safety, and cost-effectiveness. It ensures the proper installation and maintenance of cables, minimizes the risk of cable damage, supports erosion control, facilitates environmental compliance, and enhances overall project efficiency.
Transport to different job sites and increase operational efficiency by reducing the need for material transportation and processing at a central facility.
Backfill separation plays a crucial role in renewable construction, maintenance, and environmental compliance. It enhances the stability and longevity of foundations, reduces cable damage risks, mitigates erosion, and contributes to cost-effective and environmentally responsible renewable operations.