OPP-300
Shaker
The shaker motor we offer boasts bidirectional rotation capabilities. In the standard padding operations, it rotates in a clockwise direction, optimizing material screening. Conversely, for downhill padding, the counter-clockwise rotation ensures efficient clearance of materials from the shaker screen. Hydraulic actuators, positioned at the rear of the shaker system, facilitate precise height and angle adjustments, independent of the conveyor mechanism. This allows the operator to adeptly modify the shaker's elevation, particularly when operating on inclined surfaces, thereby optimizing material throughput.
Furthermore, a strategically placed vibrator beneath the spill pan can be activated to dislodge debris, proving especially effective in environments with wet or densely packed materials.
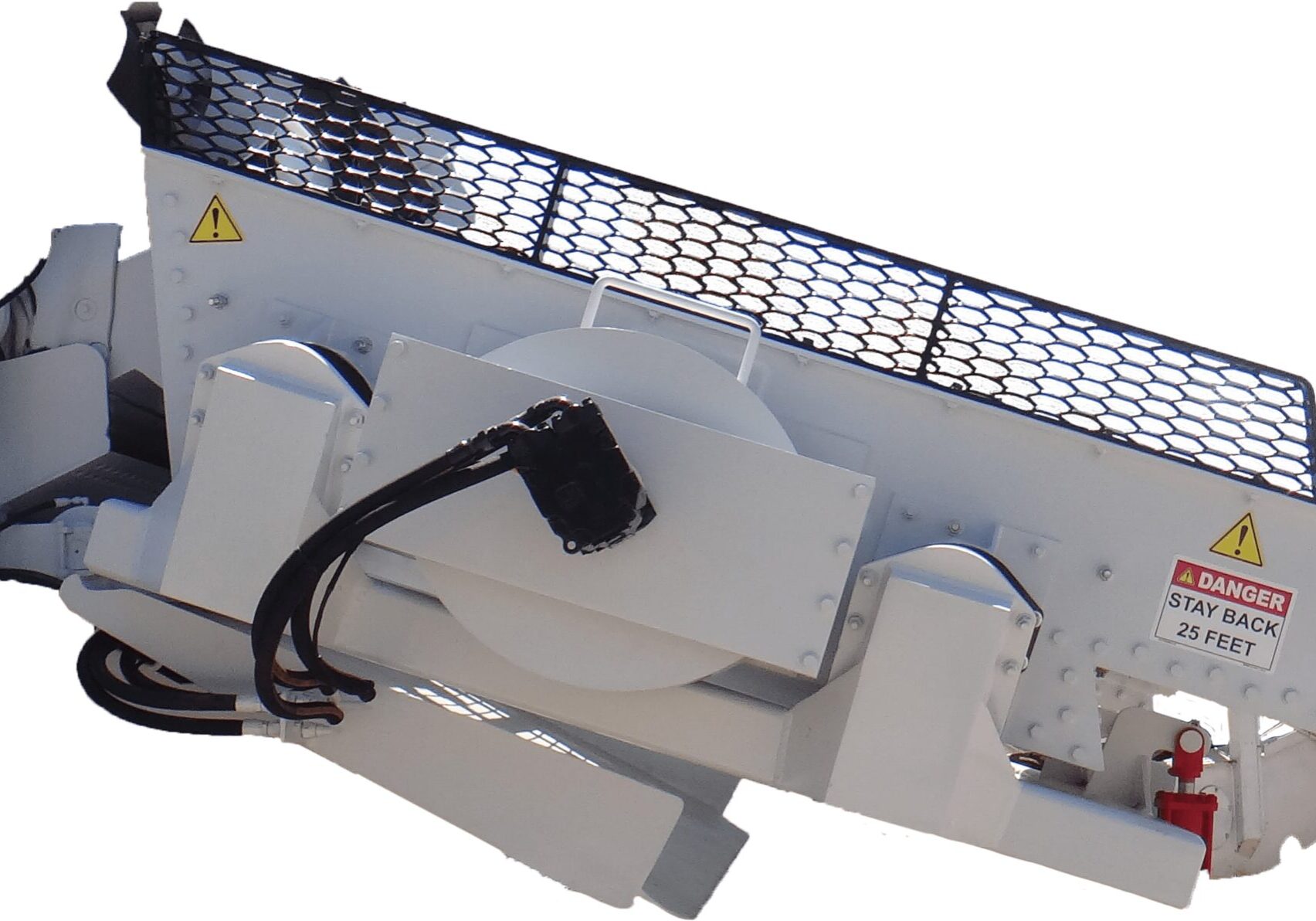
Conveyor
Leverage efficiency with our innovative bi-folding conveyor architecture. The OPP 300 conveyor features an auxiliary flexure proximate to the apex, ensuring it conforms to transportation standards without necessitating disassembly or removal.
Thanks to this advanced design, the belt is pre-mounted on the conveyor prior to transportation, thus streamlining onsite setup and minimizing deployment durations.
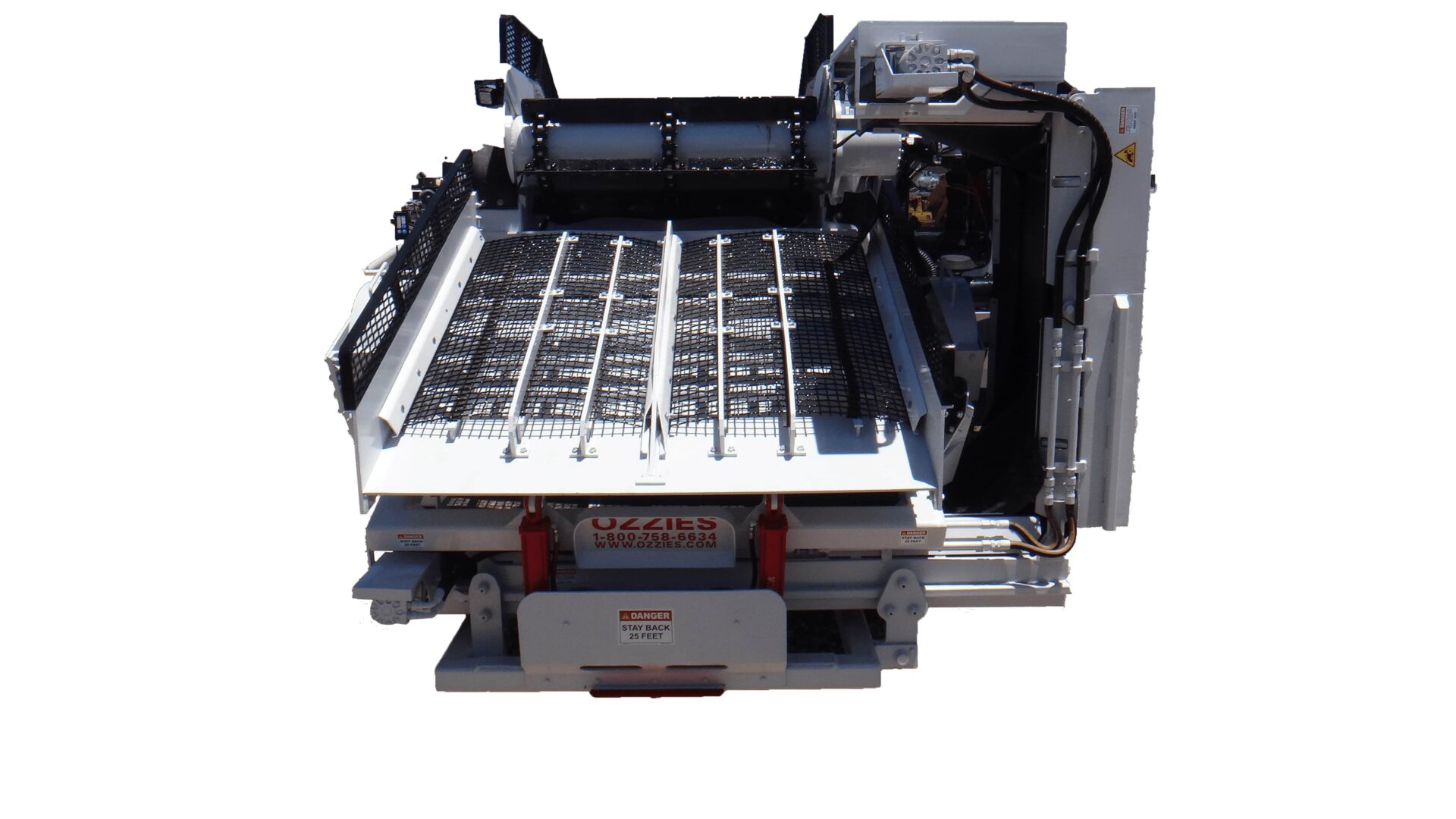
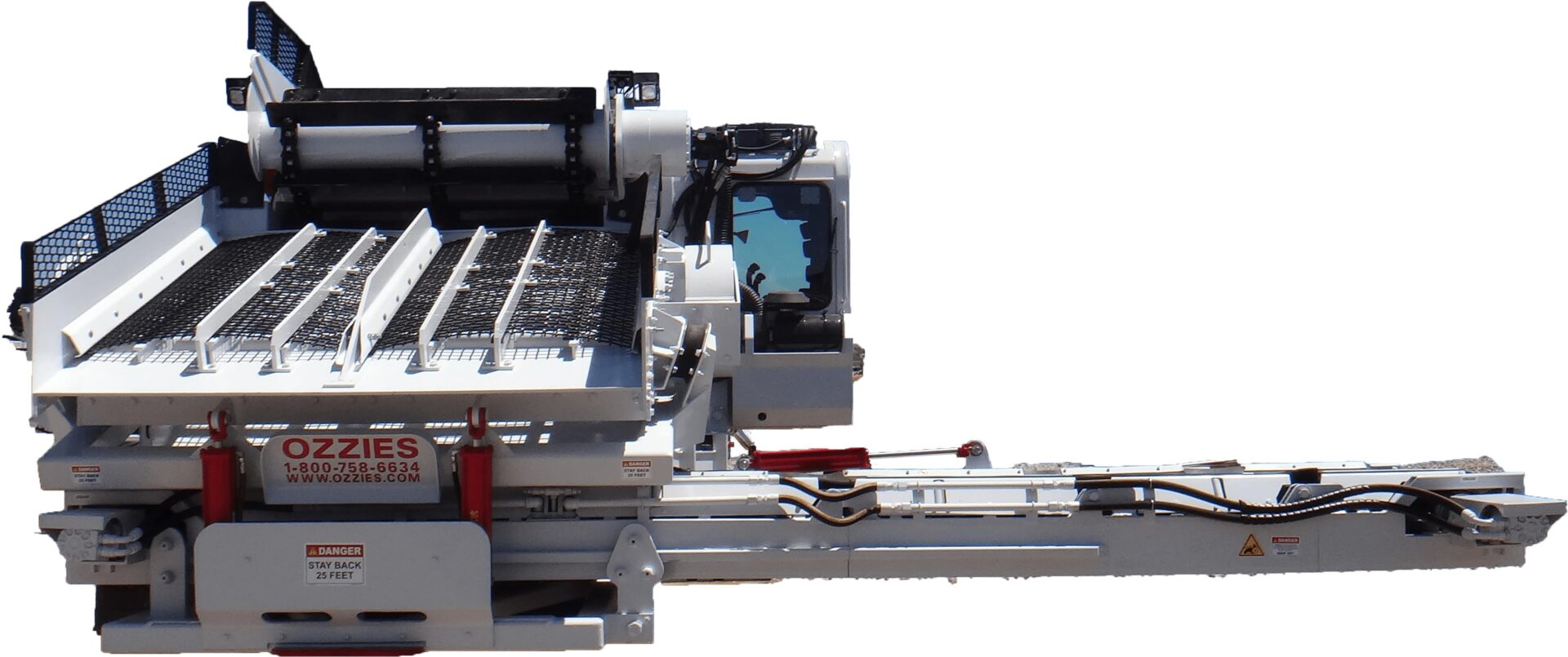
Screen Size
The OPP-300 series is designed to accommodate screen sizes ranging from 1/4" to 4", with the capability of incremental adjustments in 1/4" intervals.
Each screen undergoes rigorous accuracy evaluations, ensuring consistent and precise material filtration in every operation.
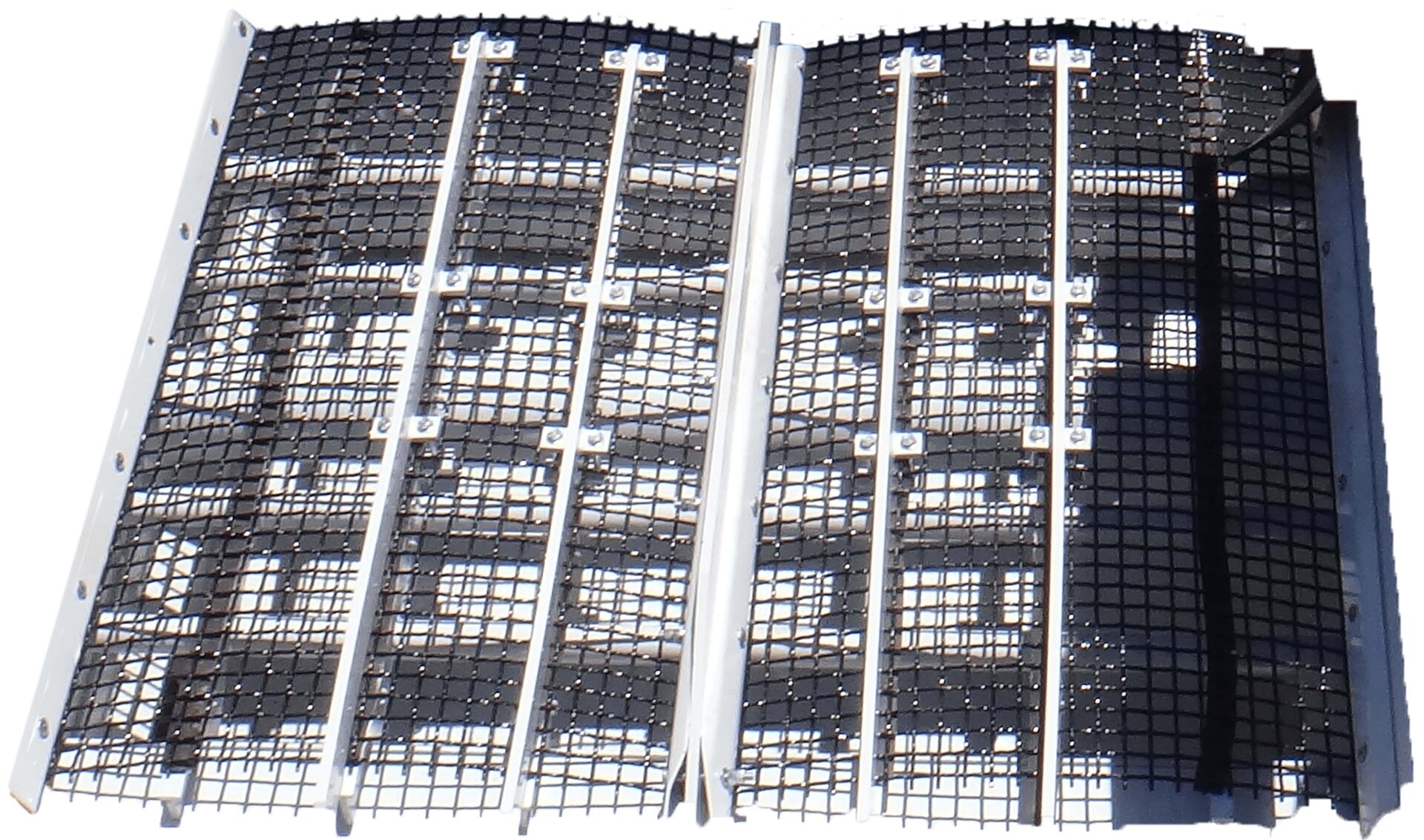
Video Monitoring System
Four high-definition, anti-glare color cameras ensure vivid imagery even under direct sunlight. The camera housings are nitrogen-purged to deter dust intrusion, and the enclosures are engineered to prevent condensation, frost, and moisture infiltration. Integrated shock absorbers mitigate the effects of impacts and vibrations, while robust protective casings shield against potential damage from falling debris.
Within the cabin, three state-of-the-art monitors provide operators with comprehensive visual coverage; showcasing views down the elevator, of the conveyor output, and the machine's left flank. Additionally, a rear-facing camera system activates an ensemble of six cameras during reverse maneuvers, enhancing operational safety.
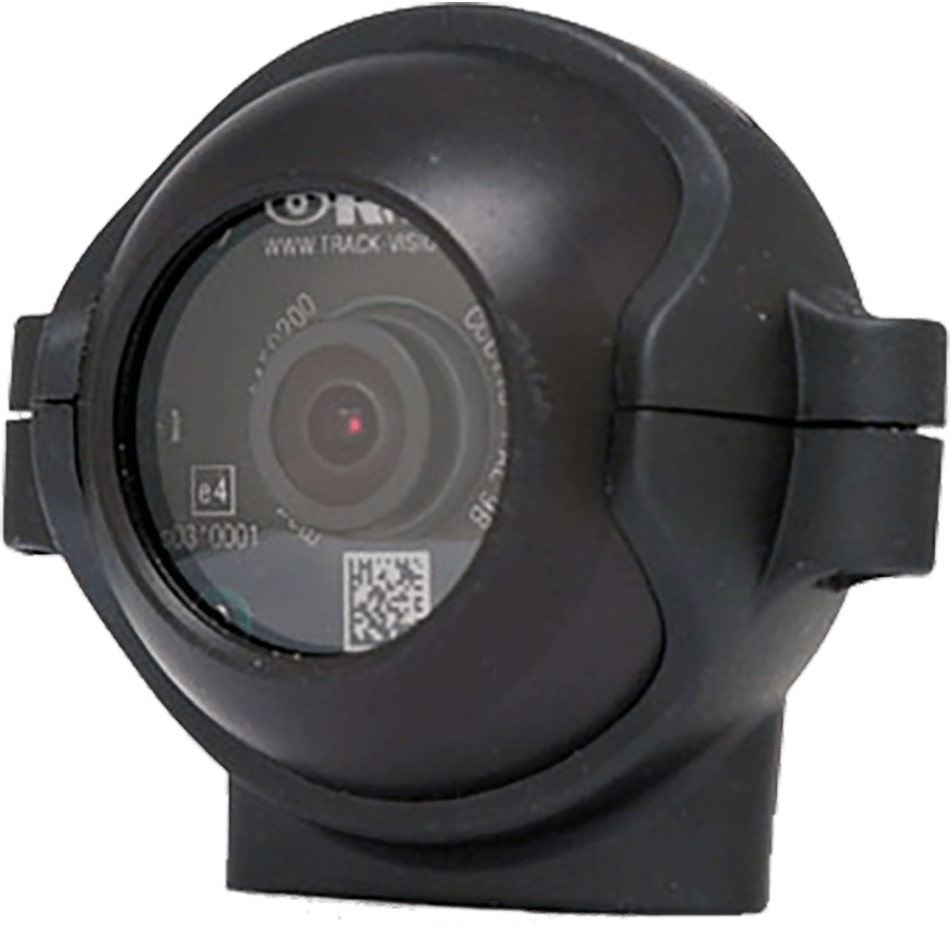
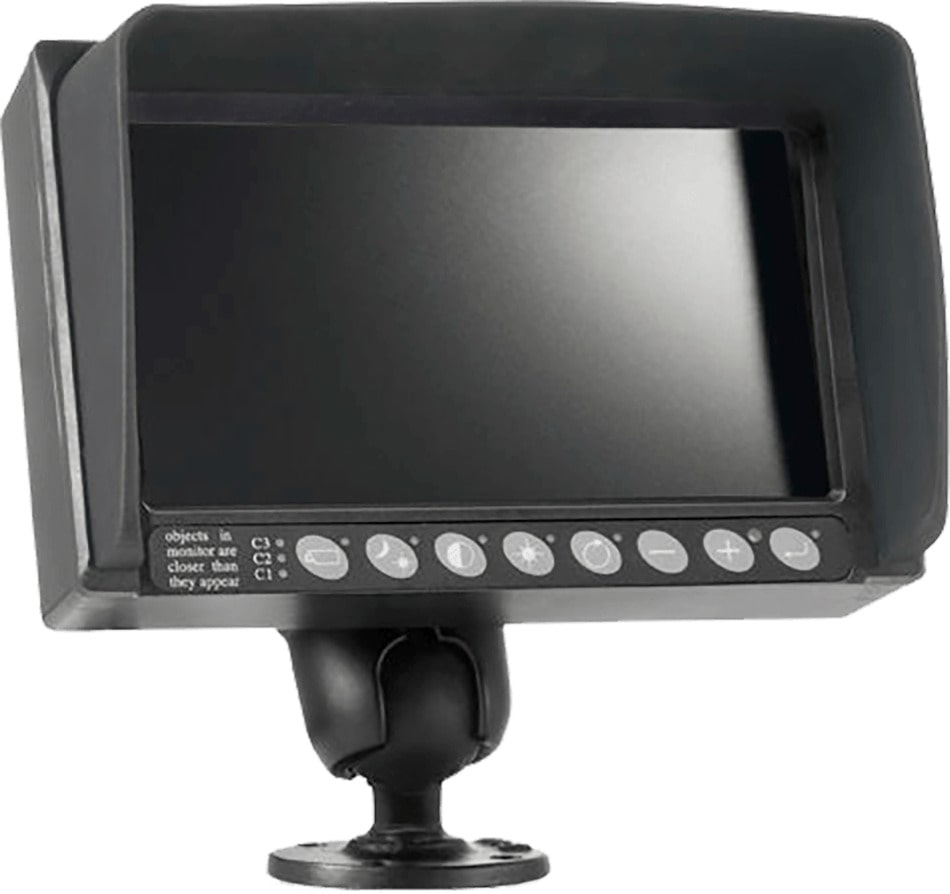
Video Monitoring System
Four high-definition, anti-glare color cameras ensure vivid imagery even under direct sunlight. The camera housings are nitrogen-purged to deter dust intrusion, and the enclosures are engineered to prevent condensation, frost, and moisture infiltration. Integrated shock absorbers mitigate the effects of impacts and vibrations, while robust protective casings shield against potential damage from falling debris.
Within the cabin, three state-of-the-art monitors provide operators with comprehensive visual coverage; showcasing views down the elevator, of the conveyor output, and the machine's left flank. Additionally, a rear-facing camera system activates an ensemble of six cameras during reverse maneuvers, enhancing operational safety.
Machine Specifications
Machine Dimensions
Transport Dimensions
Working Dimensions
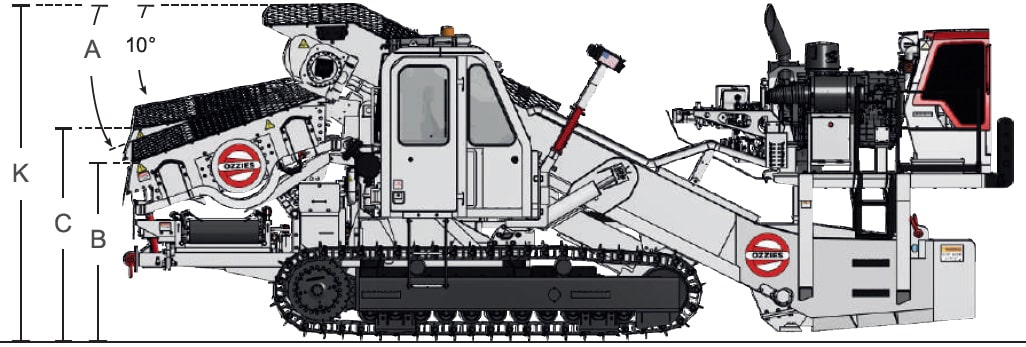
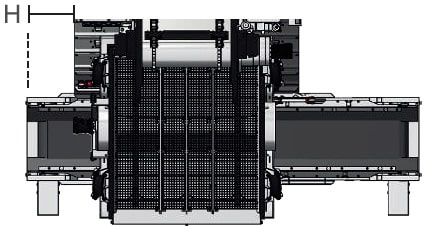
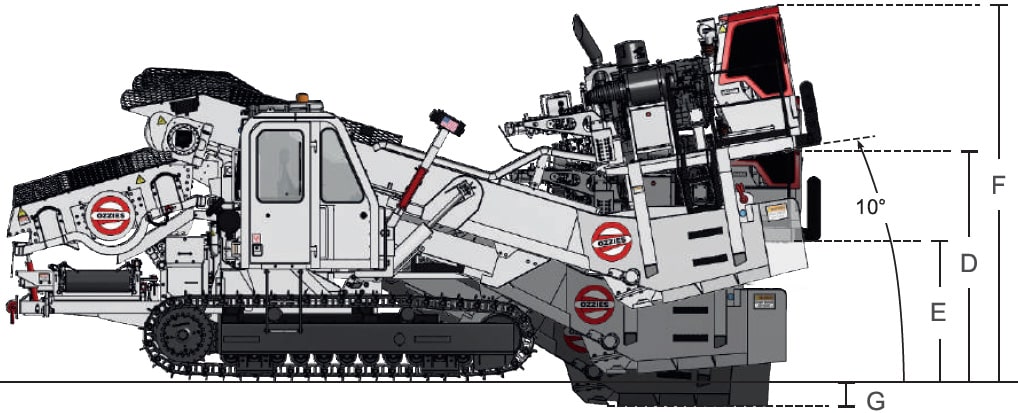
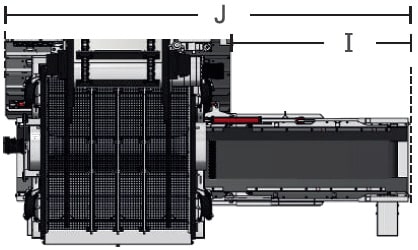
A | Maximum shaker angle from ground | 20° |
B | Minimum shaker height | 72.24" |
C | Maximum shaker height | 85.2" |
D | Raised scoop clearance | 108.96" |
E | Normal scoop clearance | 60.48" |
F | Total machine height with elevator raised | 180.84" |
G | Cutting edge diving depth | 24" |
H | Maximum conveyor reach, non-operator side | 48.72" |
I | Maximum conveyor reach, operator side | 132.12" |
J | Maximum overall width | 276.12" |
Minimum overall width | 264.96" | |
K | Height | 145.32" |
Main Applications
Backfill separation is a critical practice in pipeline projects, contributing to the reliability, safety, and cost-effectiveness of pipeline infrastructure installation and maintenance. It supports proper pipeline protection, minimizes the risk of damage, aids in erosion control, ensures environmental compliance, and enhances overall project efficiency.
The OPP-300 backfill separation system has been engineered to facilitate the backfilling process for large-diameter mainline pipelines, encompassing sizes ranging from 24 to 60+ inches (610 to 1,525 mm) in diameter.
Backfilling is a critical construction process that provides structural support, protects infrastructure, controls erosion, ensures safety, and helps achieve environmental compliance. It contributes to construction and infrastructure projects' overall success, safety, and cost-effectiveness.
The OPP-300's mobile screening technology is a valuable tool for beach cleaning, as it efficiently removes debris, enhances sand quality, controls pollution, protects the environment, improves safety, and supports the overall appeal and sustainability of beachfront areas.